– Paul Iarocci
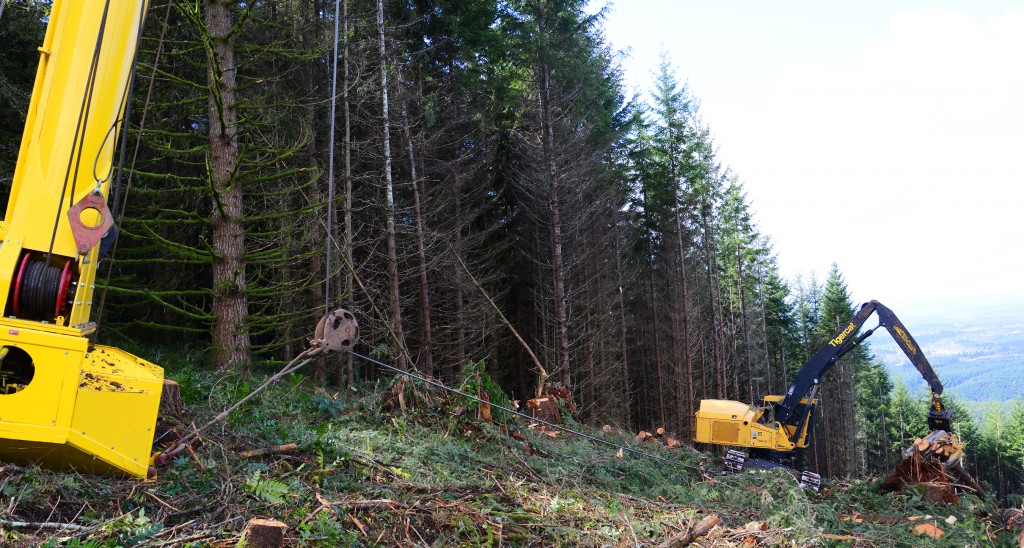
The operator controls the winch as he descends or ascends the slope, preventing sliding and allowing for downhill felling.
Based in Castle Rock, Washington, Eric Krume is the owner of Krume Logging & Excavation. He is also owner of manufacturing company, Summit Attachments and Machinery. Eric is a worker, an innovator and a dreamer. Whether he is pursuing logging, the design and manufacture of logging machinery or drag racing, he approaches the task at hand relentlessly and with singular focus and hard work.
BTB made a spring trip to Longview, Washington – a region that epitomizes Pacific Northwest logging conditions with high rainfall and terrain variability – to see Eric’s latest innovation, a fully automated cable assist system tied to the company’s latest equipment purchase, a Tigercat LS855C equipped for falling and shovel logging with Tigercat’s 5195 directional felling head. Eric, along with partner Bruce Skurdahl who works exclusively on the manufacturing side, designed and built the brand new system that was just being put to the test in April.
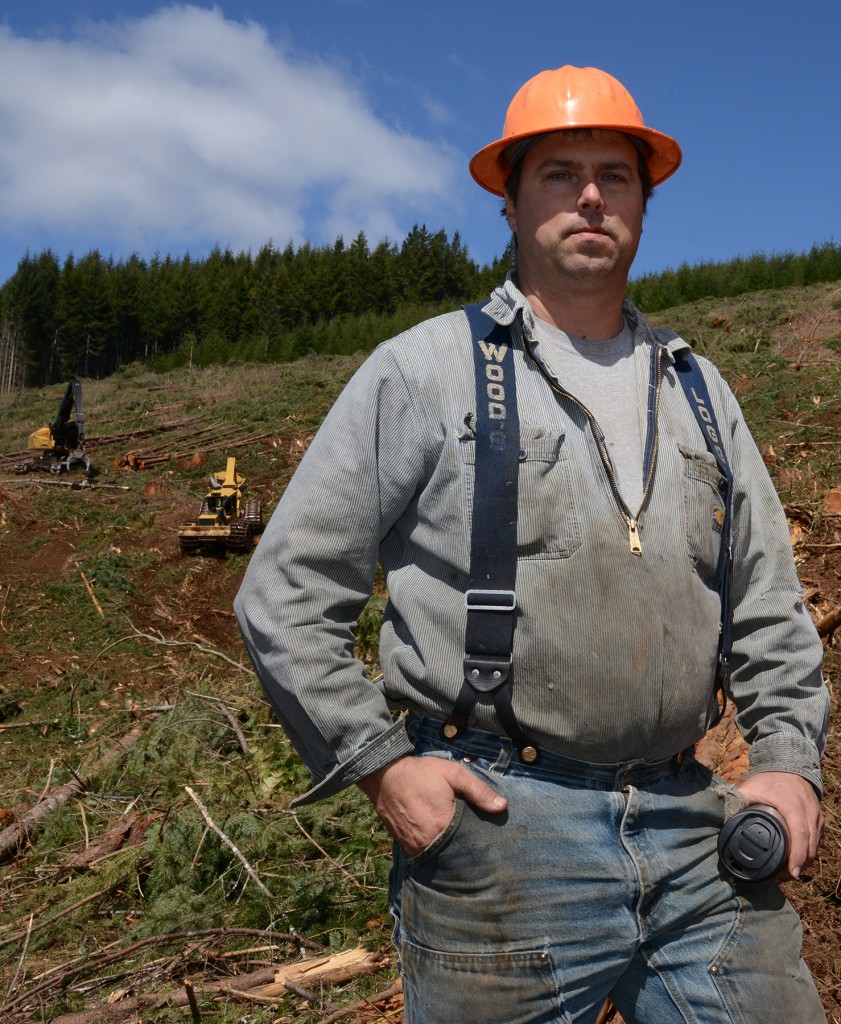
Eric Krume, owner of Krume Logging and Summit Attachments and Machinery, is a busy guy.
It is no surprise that Eric is throwing considerable time and effort into the project. Coming from a big family, Eric quit school in the ninth grade in favour of employment at a local mill. He realized very early on that the best way to get what he wanted was through hard work. He started toiling on logging crews at eighteen and parlayed his early work experiences into a successful career as a logging contractor, showing a particular aptitude for designing machines and tools to improve his own operations.
With decidedly strong views, Eric stresses that the technology has not moved quickly enough to adapt to Pacific
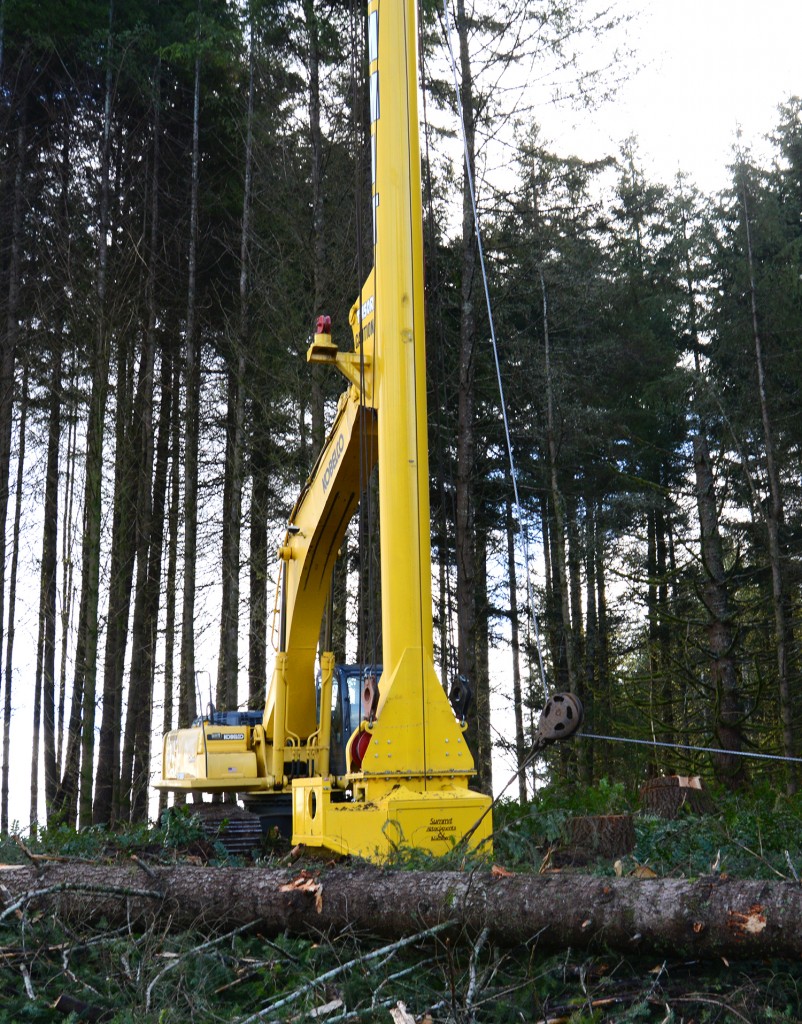
An unmanned excavator equipped with a winch and yarder tower sits at the top of the hill.
Northwest conditions and dynamics. In addition, Eric is constantly seeking out flexible solutions because of the site differences from contract to contract. These beliefs are the driving force behind his manufacturing business. In addition to the tong thrower systems that Summit is actively marketing, Eric is developing new technology based on experiences in his own logging operations.
Eric isn’t afraid to take risks or share knowledge. “I started with nothing and I have no fear to lose what I have. A lot of people, including my competitors, come to see the stuff I am doing but I don’t mind so long as I’m getting some good, honest feedback from them.” While Eric enjoys the challenges inherent in the design and manufacture process, he is also brushing up against some harsh realities, both financial and time related. As he is being pulled in two different directions with not quite enough time to devote to each facet of the business, he concedes that he can’t do it all. However, Eric’s son, Tristan, works on one of the crews and elder son, Kameron, after serving in the military is now studying engineering. Eric’s daughter Jerica is married to Garrett Lindeman who operates the LS855C shovel logger. So there is strong potential to have family step in and help out with both sides of the business in the future. While it may not alleviate Eric’s 80-hour work weeks anytime soon, it is surely a step in the right direction.
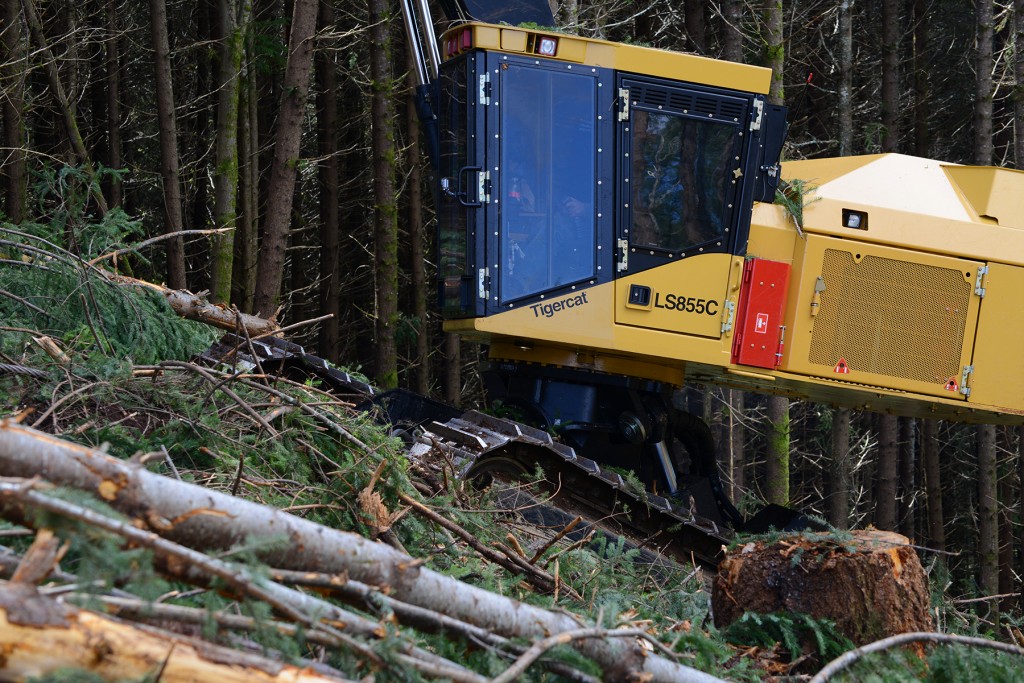
When ascending the hill there is virtually no site disturbance from the tracks. The machine climbs smoothly and easily.
Eric bought his first Tigercat machine, an L870C feller buncher in 2012 from Triad Machinery and followed up in 2013 with the LS855C shovel logger – a relatively new concept at the time. Always looking for alternatives to the norm, Eric also purchased a Tigercat 635D in 2013 but it was not an average purchase process. “Most contracts say no rubber tire equipment. Period,” Eric explains. “In the eighties and nineties, they really abused that and it was ruts and mud everywhere. When I said, hey I want to use a skidder, everybody said no. I fought tooth and nail for the skidder. I went to every company and I invited every company out.”
Included on Eric’s guest list for the demonstration were government forestry officials from the states of Washington and Oregon as well as representatives from Weyerhauser, Hancock Timber Resource Group, Campbell Global and Plum Creek. “I had three days of a demo with the skidder before I bought it. I had to make sure that the landowners would let me use it. I showed everybody that this is not your average machine and this is what we can do with it. It took me four months but everybody signed off on it.”
Shortly after acquiring the skidder, Eric purchased his fourth Tigercat machine, an 880 logger equipped for loading. But it was the concept of full mechanization and automation with a two-man crew on excessively steep slopes that drew him to a second LS855C in 2014. By this time Tigercat had sold a number of LS855C units equipped with a feller-director stick boom married to the Tigercat 5195 directional felling head for steep slope applications from Chile to New Zealand. The flexibility of the 5195 to fell large timber with a single cut and to perform double cuts without machine repositioning, coupled with the durability of the head for shovel logging, proved to be a winning concept in mountainous regions with oversized trees. On top of that, the LS855C carrier is quick, stable and agile on the slopes. Eric decided to take the concept a step further by designing and building his own automated cable assist system.
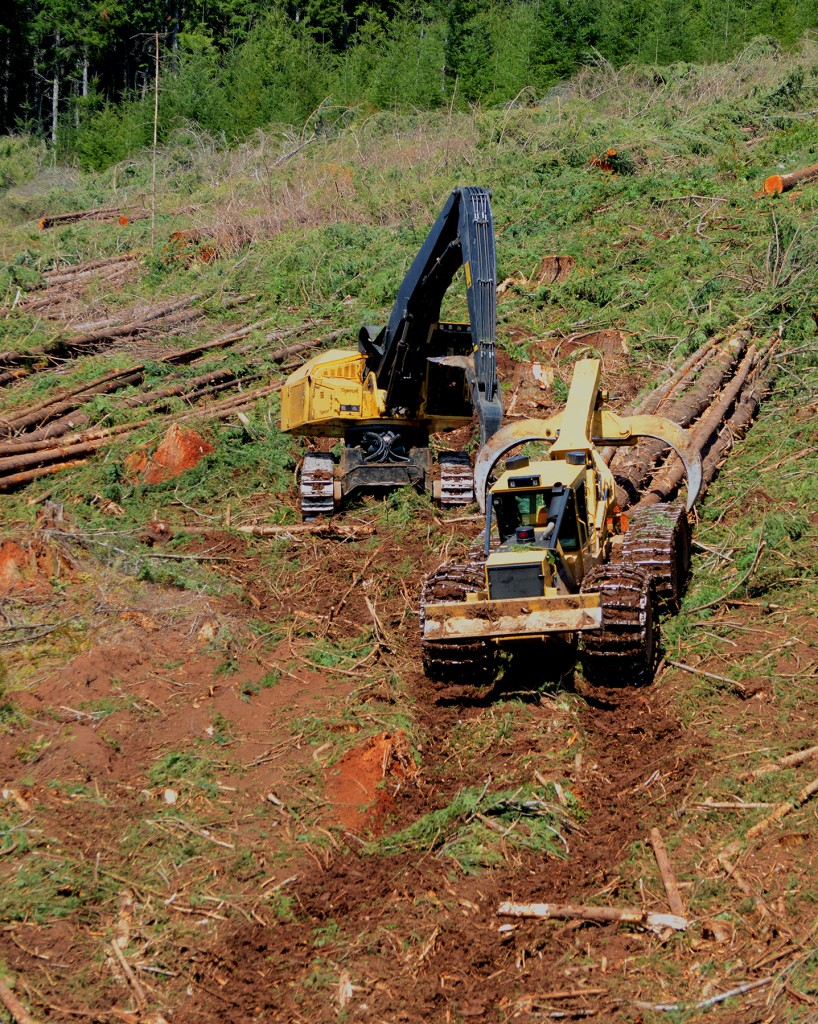
Eric fought hard to prove the six-wheel skidder concept in Washington and Oregon.
During the April BTB visit Eric, operating the machine himself, was opening up a new section of the cut block on a slope averaging about 60% and then steepening to 80%. “I wouldn’t go here untethered, he comments. “I want to tether my way into the steeper ground.” With road access at the top, the cable assist allowed Eric to work his way down the slope, while felling downhill.
The set-up
An unmanned excavator equipped with a winch and yarder tower sits at the top of the hill. A Wi-Fi signal between the two machines provides the LS855C operator with a view down the hill from a camera mounted to the excavator. The operator can toggle between this and the carrier’s rear mounted camera. A second frequency allows the operator to control the winch as he descends or ascends the slope. The cable is not timed to the tracks so some operator skill is required to time the winch speed to the track speed. The cable assist prevents sliding when descending and allows for downhill felling. When ascending the hill there is virtually no site disturbance from the tracks. The machine climbs smoothly and easily.
Although the early trials are going well, Eric concedes that he is only halfway there. “I’m missing a piece. I still have got to figure out how to get all the wood onto the truck.” Gesturing, toward the slope, he says, “Getting down there is the easy part. Knowing what to do with the wood is the hard part.”
As Eric sees it, there are a couple of problems with grapple yarding as an extraction method. First it is most economical on large-scale operations with long hillsides. “The problem I have is that I don’t have a 1.5 million dollar grapple machine and I don’t get this kind of ground a lot.” No matter how well things are going on a given contract and how well the machinery is matched to the terrain, Eric has no visibility as to the type of ground he will encounter on the next contract. Second, the systems are expensive to buy, time consuming to set up and move, and require a lot of accompanying labour.
For the test tract, Eric ended up bringing in the other LS855C and shovelling the wood up to the landing. However, on steep slopes, uphill shovel logging becomes problematic after a couple of swings as the trees lose their branches. “How do you keep the wood from fl inging down the hill?” muses Eric.
“I want to be fully mechanized and automated. With the cable assist I want to get rid of tower logging and see what I can do with a two-man crew. I already know what I can do with eight to ten men. I have not committed to falling for a yarder.” Eric envisions an automated grapple, half of a skidder if you will, attached to another machine with another drum on it. With one man falling, the second man could be processing at roadside as well as controlling the cable assist grapple machine. “I want the grapple to just take my pile of wood and go up the hill. It might go slow but if I can bring a half a load of logs with me, so what.”
Eric is quick to acknowledge that it is ultimately his people that allow him to carry on the research and development work and when all is said and done, it is the people that are most important to him. “My crew is what enables me to do all the extra things. I have always tried to train people and keep people working and it’s their hard work that allows me the time to think outside the box. I appreciate the job that they do for me and I keep focused on the fact that my company is only as good as the people in it. I want to invest in people. It’s really all that matters.”