– Paul Iarocci
Tigercat dealer, Clohse Group Lux based in Troisvierges, Luxemburg sells and services Tigercat machinery in northwestern Europe. The owners, Dieter, José and Heinz Clohse started in the industry as loggers, working alongside their father, and still operate Clohse Forestry Company with harvesting crews in Belgium.
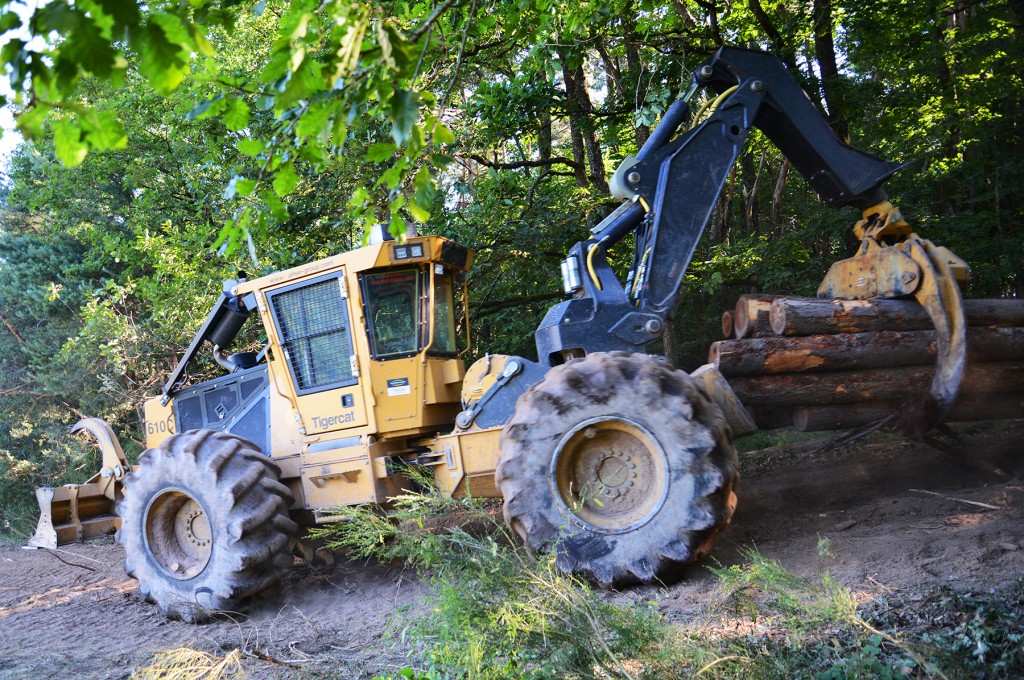
Tigercat 610C skidder fitted with a swing boom designed and manufactured by Belgium based Charlier Engineering.
However, Clohse Group’s main focus to date has been the varied regions of central and southern France, where the team has placed nine Tigercat 610 series skidders in the past few years. To achieve the required levels of service, parts support and responsiveness, Clohse Group utilizes three well equipped and capable service contractors. Feedback from the customer base has been extremely positive.
French harvesting contractors have some special constraints and requirements. Most important is the three metre (118 in) overall width limitation that is required for transport. Drive through some old French villages and you will work that one out pretty quickly. The narrow width also factors in on mountain skid trails that are literally cut into the steep hillsides. As a result, Tigercat has engineered the machine to be very narrow. This required designing a special dozer blade that allows the wheels to be kept closer than normal to the machine while still providing adequate clearance for chains and axle oscillation. Tigercat also designed and factory installs the front blade grapples that are required for every 610 skidder sold in France.
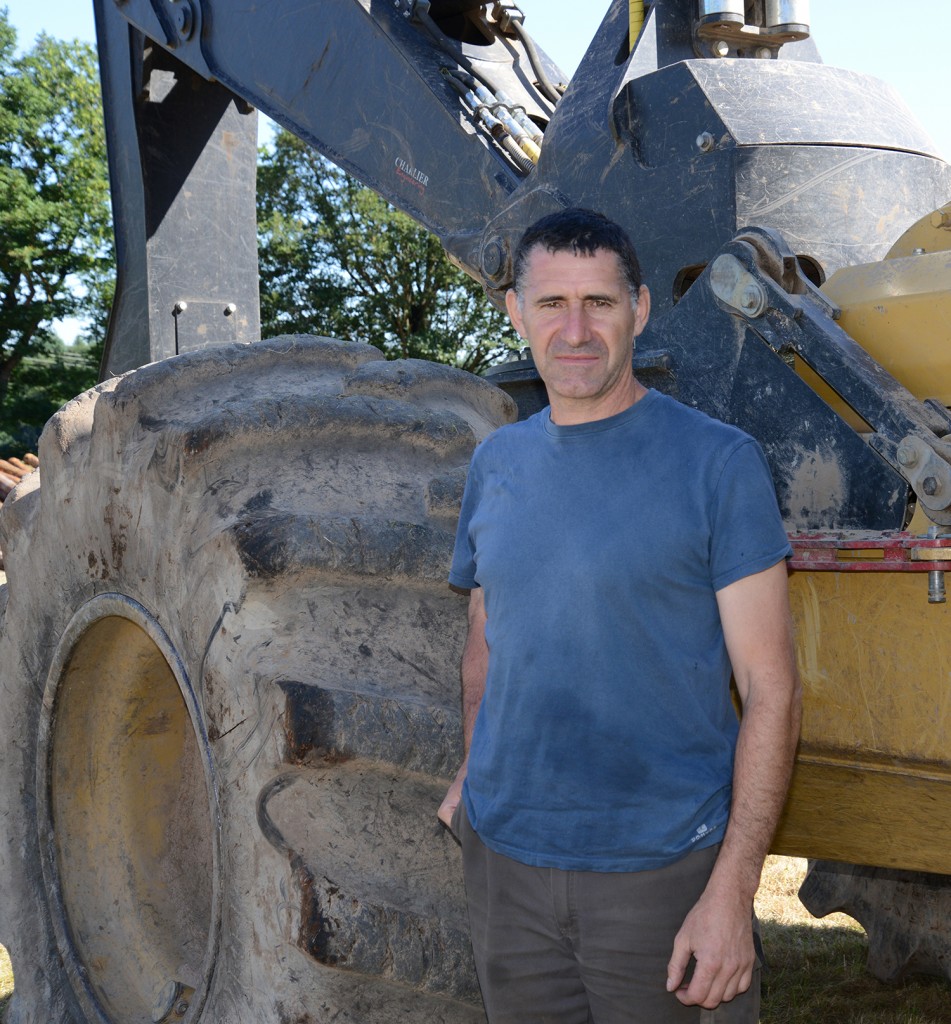
Bernard Fouilland, owner and operator of the 610C swing boom skidder operating in the Charolais region.
Essentially there are four variations of the base model that are sold in different regions of the country. The first is a standard dual function arch machine with remote control just for the winch. Second is the swing boom skidder with full remote control. The swing boom itself is manufactured in Belgium by Charlier Engineering, a small engineering company that also designs and builds harvesting heads and a four-wheel drive harvester for markets in western Europe. Dual rotate motors and a large, robust bearing provide ample swing torque and lifespan. In addition to high quality machining and welding, special care has been taken in the design to ensure maximum component commonality and minimal rework. The well-engineered and constructed boom accepts the standard pin connections in the rear chassis of a Tigercat skidder. The rotator, snubber and grapple are standard Tigercat issue.
The third variation is used exclusively in the Rhone-Alps and Auvergne regions. The DW610E mountain skidder with full remote control is equipped with a double drum winch. A Clohse appointed service contractor Foretmat, headed by François Lacroix and situated in Novalaise, Haute Savoie fits the winch hardware. In addition, the company designs, fabricates and fits the winch backboard and fairlead system according to customer preference. The fourth version of the 610 is the dual winch machine, additionally equipped with a 7,2 m (23 ft) 114 kNm Palfinger crane mounted between the winch and the cab.
The swing machine
The first machine to be equipped with a swing boom is owned by Bernard Fouilland who operates in the Charolais region, well known for the beef derived from the white Charolais cattle that graze the area’s rich pasture land. Bernard operates alone, contracting out felling duties either to hand fallers or a wheel harvester subcontractor depending on the forest and terrain conditions.
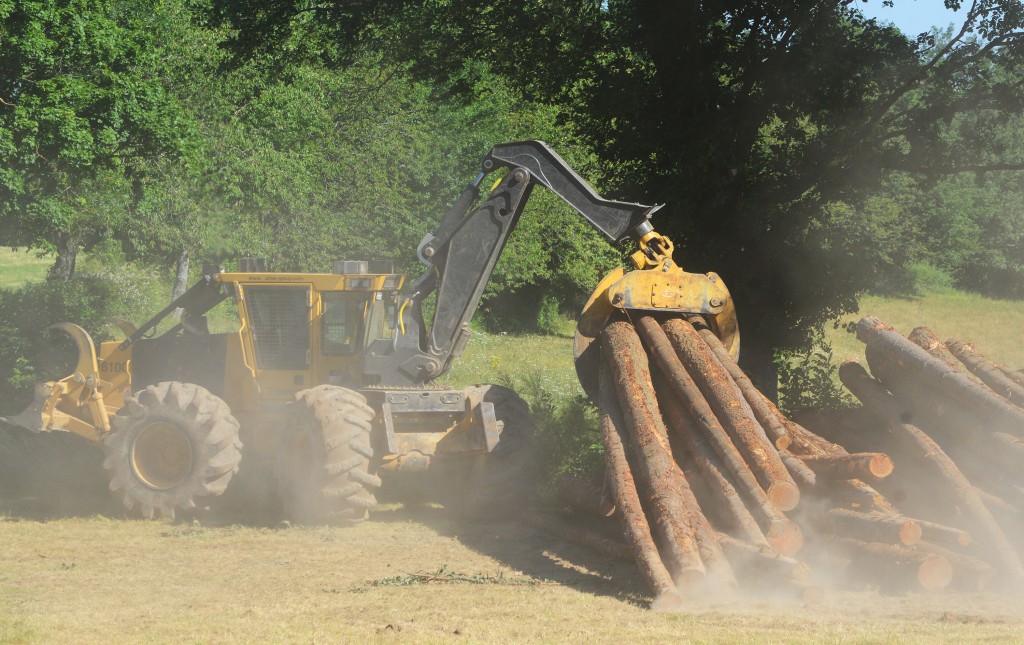
The swing boom makes it quicker and easier to build high decks when space is limited.
With average production up to 400 m³ per day (one cubic metre equates to approximately one ton), Bernard’s tracts are characterized by steep slopes, long skids and very small clear fell harvest areas yielding 700-1 500 m³. Often the terrain requires Bernard to use a combination of cable and grapple skidding, cabling the logs out of the most precarious areas, before building bunches for grapple skidding to roadside. (This is why the remote control of the machine and winch is required.) Whether manually or mechanically felled, the trees are always skidded to roadside without limbs and always bucked in-stand to a sixteen metre (52 ft) maximum, a transport length limitation. It is advantageous for Bernard to follow a mechanical harvester that can prebunch the wood, although the swing boom is an excellent tool for quickly building bunches.
Of the four skidder variations in France that Clohse Group is promoting, the swing boom seems to be the configuration with the most potential to help contractors in other parts of the world. The ability to bring the load alongside the machine comes with many advantages. First, it facilitates much quicker cycle times when double bunching. Rather than overshooting the second bunch and backing the load over it so that the bunches cross, Bernard just drives alongside the target bunch, releases the bunch from the grapple, picks up the new load and off he goes. Gathering loose stems and building bunches from scratch is also much quicker compared with a dual arch machine.
When operating on slopes and traversing side slopes, Bernard uses the boom to manipulate the load, changing the centre of gravity. This improves the stability of the narrow machine and also acts to reduce stress on the structure and axles. (Bernard notes that he would prefer a wider machine for his application but transport rules do not permit it.)
Another terrific advantage, especially in tight roadside scenarios is the ability to quickly deck the wood quite high with less effort and machine movement than a standard grapple skidder. In general, the swing boom prevents direction changes, blading and other time consuming motions, improving the flow of the operation.
Bernard has made some clever modifications that suit a one-man operation. One example, he installed an automated fuel system with an electric pump and switch on the machine so that he can refuel while performing other maintenance tasks to increase his daily productivity.
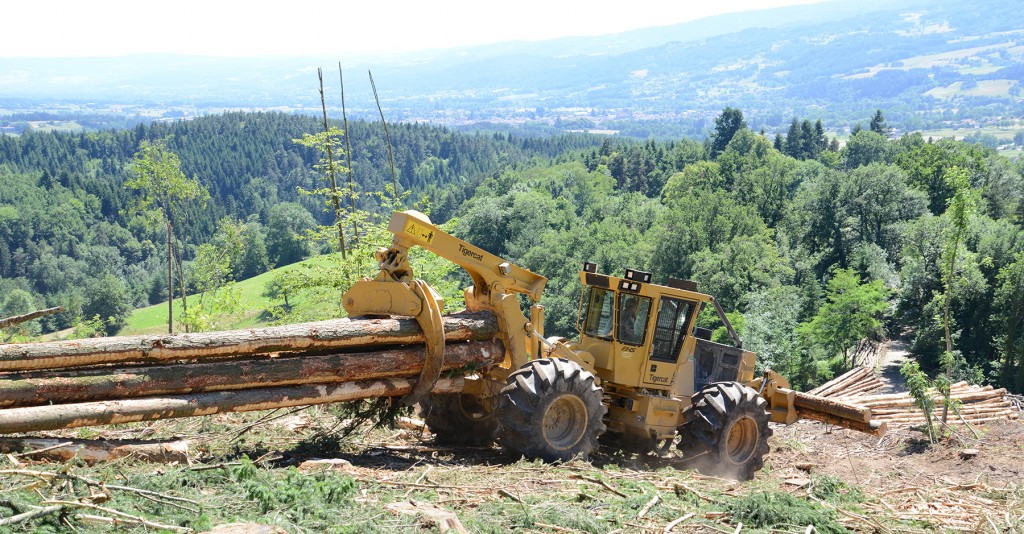
The 610E grapple skidder equipped with front blade grapples for sorting logs and transporting shortwood.
Dual arch
The next operation BTB visited was that of Christian Ricoux, owner of a 610E dual arch grapple skidder equipped with front blade grapples. Christian operates in the Auvergne region of central France. His terrain is usually quite steep with species and length sorts on tracts with very limited space along the roadside and no real landing area.
Felling is generally split evenly between manual and mechanized and all trees are limbed and bucked in-stand to maximum sixteen metres (52 ft), so Christian too must deal with skidding the random length shortwood. Typically he will work in mixed forests with species such as beech, acacia and douglas fir. To deal with the random short logs, Christian will grab a bunch with the front blade grapples while skidding a load of long logs. He also utilizes the front grabs for sorting and decking the logs in the tight quarters at roadside.
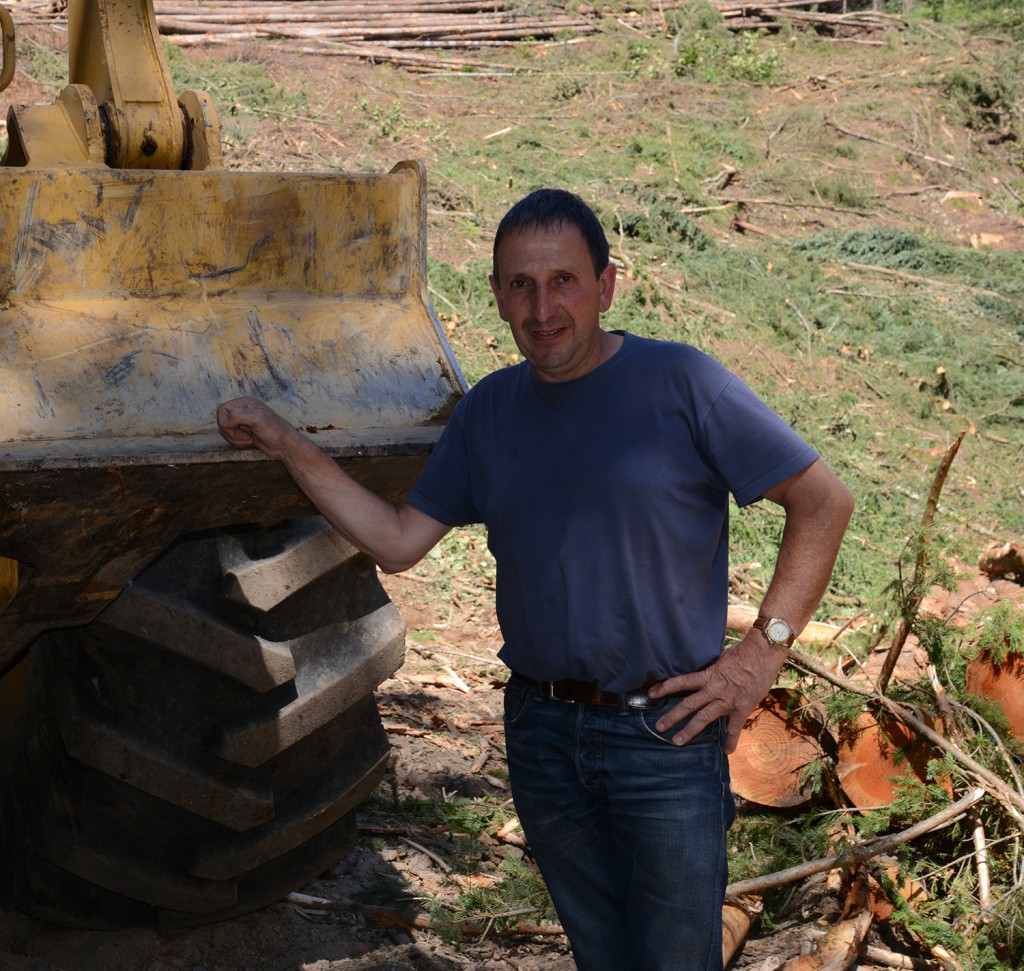
Christian Ricoux owns and operates the 610E grapple skidder.
Mountain logging in the French Alps
Next stop was the Rhone-Alps where double drum winch cable skidders have reigned supreme for decades. This unique configuration includes the front blade grabs along with a dual drum winch mounted on the rear chassis with the fairleads integrated into a large hydraulically moveable backboard that can be lowered below grade to act as an anchor when the machine is actively winching. When the machine is skidding, the logs are pushed up against or sitting on top of the backboard, depending upon the design.
Clohse Group technical manager, Piers Eyre-Walker explains that one of the big advantages of the Tigercat skidder over others in the market is the winch control. Excellent electronic coordination between the clutch, brake and drive results in virtually no slack and perfect control as the winch drive starts and stops. “It is one of those subtle things that you take for granted when you have it, but is very important and no one else has it. All the others tend to slip back a little when the operator stops winching.”
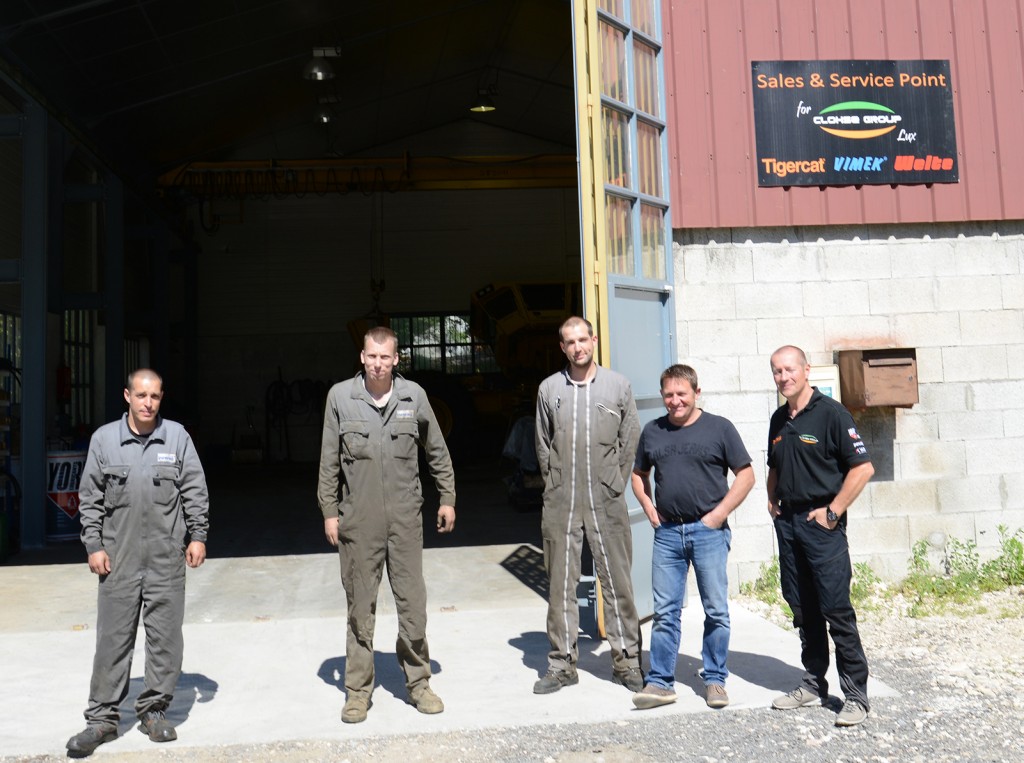
The technical staff of Clohse Group appointed service contractor, Foretmat, headed by François Lacroix (second from right), situatedmin Novalaise, Haute Savoie. The facilities are well equipped.
The Alps differs in other ways from the logging operations in Central France. There is virtually no clear felling and nearly all thinning is performed manually. There are likely around 200 double winch skidders working in the region supplying slow growing, extremely high value wood to local sawmills. The trees are large and valuable. A single stem could measure 15 m³ and values range from $200-700 per m³. Due to high snow accumulations, there is no harvesting activity in winter. Owners and operators alike do other work during winter, often related to the ski industry.
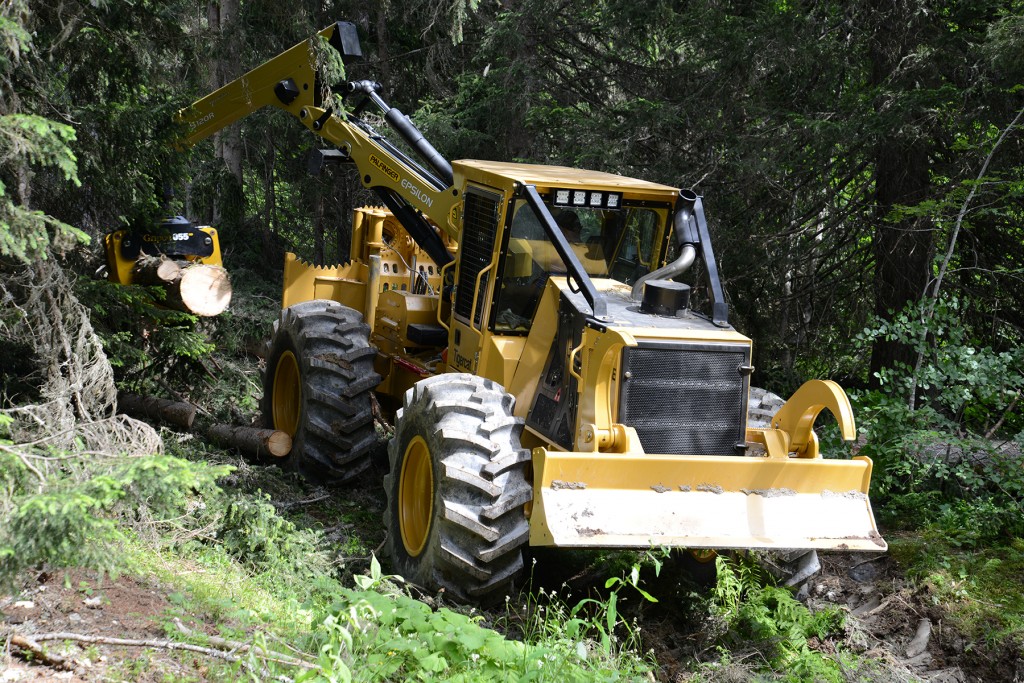
Nicolas Gombert recently took delivery of his first brand new machine, a crane equipped DW610E skidder.
Nicolas Gombert, who recently purchased his first brand new machine, a DW610E equipped with a Palfinger crane, is a French chainsaw sculpture champion who operates Sculpture Glance & Bois, a business that creates wood and snow sculptures for many private and corporate clients.
Nicolas purchases private timber and markets the wood himself, picking up tracts where he will harvest as little as 700 m³. He averages 100 m³ per day including felling, limbing, bucking to 14 m (46 ft), skidding and sorting. He will use the crane to reach trees that are close to the skid trail and will winch out the logs that are further away. Another common practice is to winch the machine up or down extremely steep slopes to access the downed timber, France’s version of tethered logging.
Sorting with the crane really improves productivity because it is very difficult and time consuming to sort with cables and the blade. Also because of the high value of the wood, the logs must be handled very carefully. The hand fallers take the edges off the butt of each log so that it rides over obstacles on the forest floor more easily when winching. The remote control system saves the operator, who also chokes the logs, a great deal of back and forth time between the cab and the end of the cables.
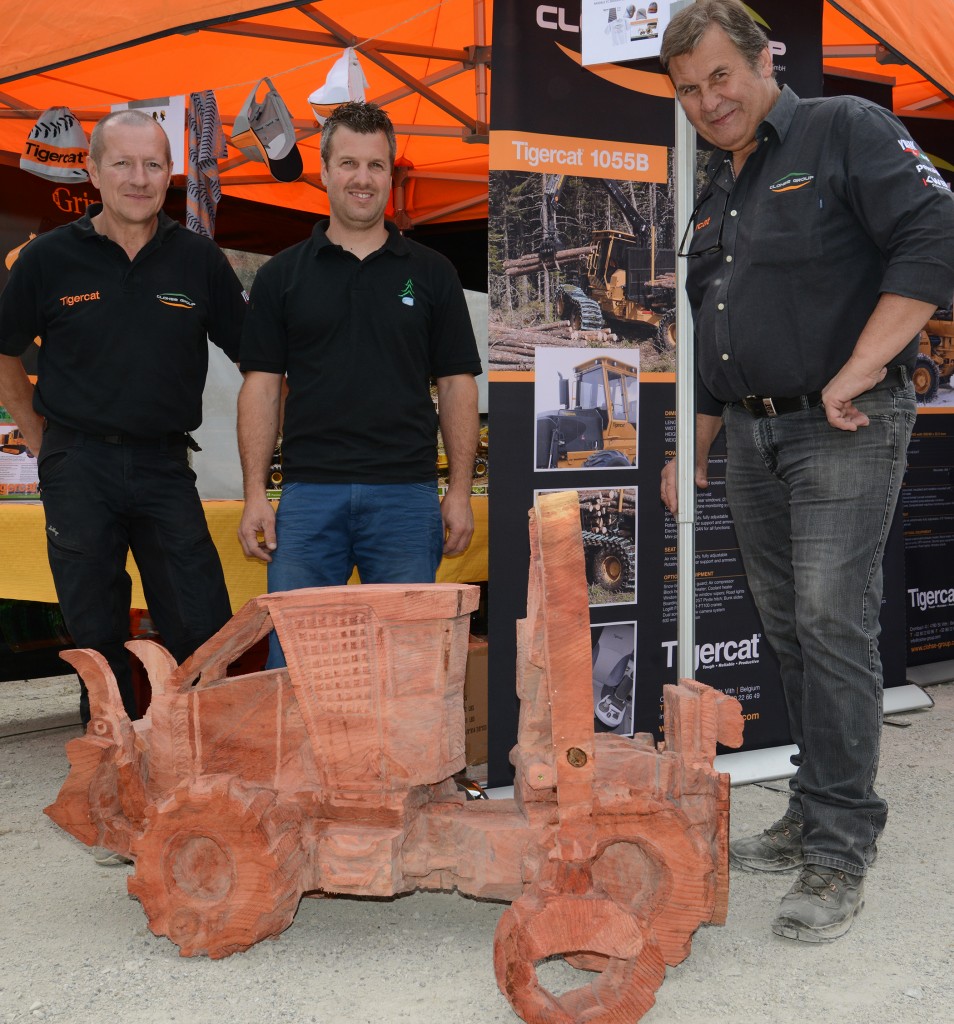
Nicolas Gombert (centre) was so excited about his new skidder, he recreated it in cedar. He is flanked by Clohse Group technical manager, Piers Eyre-Walker (left) and Clohse Group owner Dieter Clohse.
For this machine, the first to be equipped with a crane, Clohse added a second IQAN system for the crane functions and modified the Turnaround® seat so that it rotates a full 360 degrees with electric rotate control. The pedals are fixed to the seat turntable and rotate with the operator. Like a forwarder, this allows the operator visibility when using the crane at any angle. It also allows the operator to use either door, a big advantage in cable skidding applications where the operator is entering and exiting the cab in difficult ground conditions.